Infundibuliforms
responsive envelopes: Kinetic Tensile Surface Environments
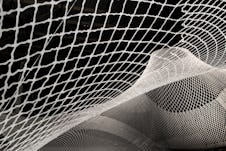
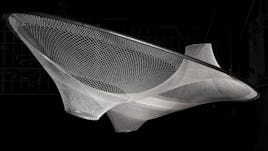
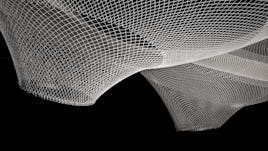
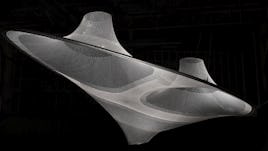
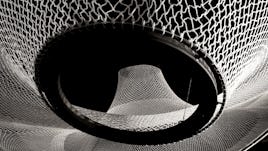
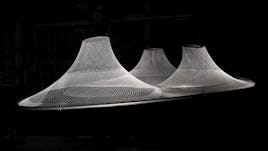
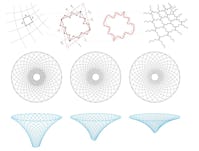
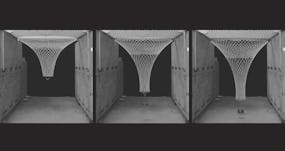
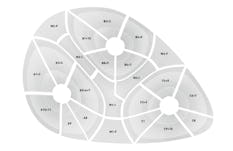
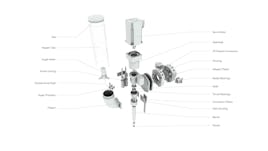
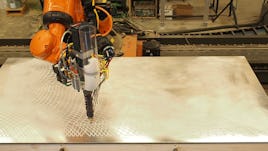
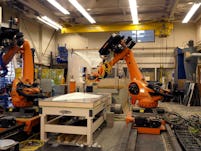
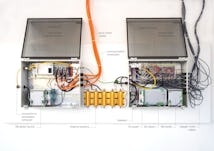
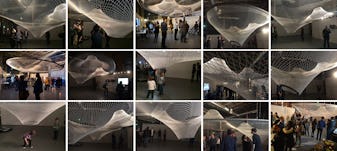
Infundibuliforms advances research in lightweight, kinetic surfaces that have the capability to create spatial enclosures with minimal amounts of material and that are able to dynamically adapt at low energetic cost. Since the middle of the last century, there has been increased interest in adaptable structures involving motion systems, or, as Frei Otto and his colleagues preferred to call them, “convertible” structures (Otto 1972). This prototype-based research uses cable robotics to deform a tensile 3D printed cable net surface. The work advances three parallel trajectories in computational, fabrication, and geometric research.
• The development of a dynamic model to both simulate and control operation of the physical system in real time.
• New tools and methods for robotic additive manufacturing to enable the 3D printing of thermoplastic elastomers for tensile surfaces.
• A geometric methodology for developing cable nets that could be loaded to produce tailored catenoid forms using spring-based simulation methods.
Digital Design Environment
Dynamic simulations are increasingly being applied in robotic control applications as they have the potential to create a 1:1 relationship between the physical system and the simulation. The work developed custom Grasshopper code that utilizes the Kangaroo physics engine to actively visualize possible forms of a tensile surface. Another Grasshopper plugin was developed to allow Ethernet-based communication between the physics simulation/design environment and the TwinCAT motion control software. TwinCAT’s industrial platform was chosen over more common microcontroller based systems as it uses IEC 61131-3 programming, which is standardized across all industrial control systems, as well as the PLCOpen standard, which supplies hundreds of standard motion blocks. This makes the system inherently scalable and portable to other platforms. These advancements in the computational simulation and control environment expand the possibility for designers to fluidly explore virtual and physical prototyping and operation of deformable structures.
Robotic Thermoplastic Elastomer Extrusion
In order to produce the tensile surface, the team pursued the fabrication of a monolithic elastic net fabricated through robotic extrusion of thermoplastic elastomer (TPE). To enable the manufacture of the surface, an existing polyolefin extruder was modified to include a hopper for pelletized thermoplastics and mounted to a 7-axis robot. The liquid TPE is deposited onto a heated aluminum bed to facilitate joint fusion, and then allow to slowly cool into a monolithic textile surface.
Flat-to-Form Geometry
The geometric challenge of this project was to create an elastic cable net geometry that could be extruded onto flat surfaces and that could then be stretched into the desired anticlastic forms. In order to achieve more specifically tailored forms, we developed a method that maps the target three-dimensional mesh edge length onto the flat-printed geometry by introducing curvature into the line and that uses a spring-based physics to “grow” the desired edge length into the geometry of the line.
Prototype Installation
A full-scale prototype testbed has been fabricated and installed. It consists of a 30m2 tensile polymer cable net surface spanning between an outer ovoid ring and three weighted inner rings. Three universally encoded stepper motors control the tilt of the outer ring, and three triangulated sets of custom-built servo motors position the weighted rings located at the end of each infundibulum. These dynamically reconfigure the surface between vaulted and chimney forms within a broad range of positions. The testbed has been used to refine the 3D printing technology as well as the simulation and controls environment.
References
Otto, Frei (ed.). 1972. IL 5 – Wandelbare Dächer / Convertible Roofs. Mitteilungen des Instituts für Leichte Flächentragwerke (IL), Universität Stuttgart.
Typology | Kinetic Tensile Surface Environments |
2015-2016 | |
location | Ann Arbor, MI |
SCALE | 300 square ft |
scope | Lightweight kinetic surfaces that have the capability to create spatial enclosures with minimal amounts of material and that are able to dynamically adapt at low energetic cost |
Team
RVTR | Geoffrey Thün, Kathy Velikov, & Daniel Tish |
Matter Design | Wes McGee |
Fabrication Assistants | Asa Peller, Dustin Brugman, Andrew Kremers, Andrew Wald, Iram Moreno Pinon |
Technical Partners | Buckeye Polymers, Industrial Fabricating Systems, Beckhoff |
Awards | gRANTS
- Research Through Making Program | 2016 Taubman College of Architecture and Urban Planning, University of Michigan
- Small Projects Grant | University of Michigan Office of Research